Digitally transform operations of field technicians, design & planning team to reduce overall MTTR by 45%
Most of the Digital Service Providers (DSPs) are struggling with the rising cost of repeat-dispatch and a higher Mean Time to Repair (MTTR). As it takes a longer duration to repair faulty hardware, this impacts customer experience leading to a higher probability of churn. According to Forrester, 73% of customers consider time as the most critical point of customer service.
To schedule an efficient dispatch of repair activities, spare parts information becomes critical. It is not only the right delivery of spare parts that matters, but also the delivery at the right place at the right time. However, the existing approach of managing and finding spare parts involves high manual activities, lacks automation, and doesn’t have any real-time updates.
Major roadblocks for DSPs in accelerating repair activities
- Element of unpredictability – Less visibility on what is available in stock vs onsite requirements.
- Inefficient monitoring of spare parts movement & storage across location – Lack of real-time reports on the availability of spare parts.
- No optimized routes to reach warehouse location – This gets further complicated when a technician needs to visit multiple locations to complete multiple work orders.
- Communication hurdles and poor synchronization – Repeated callbacks, late arrival, lack of clear visibility and transparency brings down process efficiency and impacts customer satisfaction.
Accelerating MTTR requires DSPs to adopt solutions that can digitally transform the operations performed by field technicians and design & planning team.
DSPs can build spare-location intelligence framework to fast-track repair activities
Fig: Spare-location intelligence framework
This article details each of the key elements of the framework and showcases how these elements digitally transform the dispatch operations.
- Heat map of spare locations – Provide real-time visualization of spare parts availability at different warehouse locations
Building a heat map with the below recommendations enables field technicians to quickly get all details in a single click, which otherwise takes 1-2 hours just to find spare availability.
- Create quick search options – Technician can search the spare parts by entering any one of the search criteria.
- Integrate advanced search functionalities such as image recognition and bar code reader into the mobile app to ease and fast-track the process.
- Route optimization- Maximize the number of ticket closure by finding dynamic service routes on a continual basis
This should direct field technicians along the best route to accomplish maximum tasks as per the allotted work orders. Following recommended mobile-based features for field technicians can lead to a 45 – 50% increase in job completion rate.
- Get optimized routes to nearest 4-5 locations – Field technician can then select one of the locations based on miles count, customer location, and location of other scheduled work orders.
- Find dynamic routes to selected spare locations – Provide the most optimized route within the app to reach the spare location.
- Reserve spare parts in advance – Very often the field agent doesn’t get the required number of spares when he has reached the location. Features such as “advance reservation,” notify the warehouse manager to block any movement of the spare parts.
- Self-locate the spare parts in the warehouse – Having information such as shelf number, rack number, and bin number help field technicians to self-locate these spare parts when they have reached the warehouse.
- Integrating analytical chart views with spare locations – Adequately manage the storage and movement of spare parts across different warehouse locations
The planning team needs to ensure that spare parts are always available at the right place and in the right quantity. Integrating features such as analytical chart views along with the heat map of spare availability can further ease planning decisions.
- Identify which spare part is understocked and at what location
- Monitor change to reallocate spare parts
- Ensure higher availability of spare parts at locations where demand is higher
- Understand trends and set priorities
In addition to this, integrating spare locations with real-time GIS (geographic information system) data can reveal real-time insights into data, such as weather patterns, trends, and situations – helping planning teams to make prudent decisions. This helps the planning team to identify risk-prone areas and take precautionary measures to respond to any events.
- Real-time reports, tracking, and alerts – Keep transparency on spare parts availability & overcome communication hurdles
- Real-time reports are a single source of truth for decision making. This avoids discrepancies leading to understocking or overstocking of spare parts.
- Overcome communication hurdles by going digital – Ensure live tracking, email alerts, and notification features are available to the field manager and the technician.
Important features for field manager
- Get technician location and their availability at any point of time to better prioritize work orders
- Decide whether to bring an additional resource to supplement workload
- Gain control of late arrival and rescheduling situations
- In case of any delays and postponement, provide alerts to the customer in advance
Important features for field technician
- Digitally be in sync with the rest of the team to get real-time updates and reduce callbacks
- Notify customers in real-time of arrival status
Business & operational benefits achieved by a leading Digital Service Provider (DSP) in North America
The DSP was facing challenges in reducing overall MTTR, which led to poor customer satisfaction. Owing to the opaque nature of operations, it was difficult to fast-track repair activities. Implementing spare-location intelligence helped the DSP to achieve the following major benefits:
- Reduced overall MTTR by 45 – 50%
- Increased analytical capabilities helped the design & planning team to make a better decision
- Reduced field agent’s time taken to locate spare parts by up to 70 – 75%
- Improved customer experience and Net Promoter Score (NPS)
By Muthukumaravel S
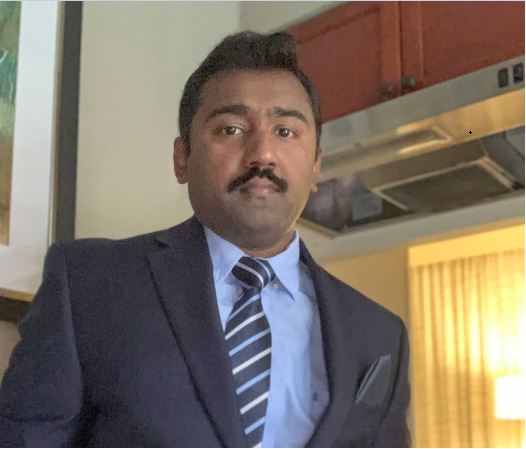
Senior Director, Prodapt Solutions
Muthukumaravel is a hands-on technology leader with 15+ years of consulting experience. He has a commanding knowledge of network engineering including provisioning, operations, management of system architectures, and implementation. He is passionate about implementing solutions that rejuvenate Telcos/DSPs (digital service providers) through Platform and Network modernizations, and cloud automation.
Muthu is the Senior Director at Prodapt, a two-decade-old consulting & managed services provider, singularly focused on the telecom/DSP ecosystem that helps clients transform their IT, products, operations, and networks to meet their strategic objectives.